Will the Semiconductor Market be worth $1 trillion by 2030?
Digital transformation may become the driving force in securing a projected $1 trillion semiconductor market by 2030.
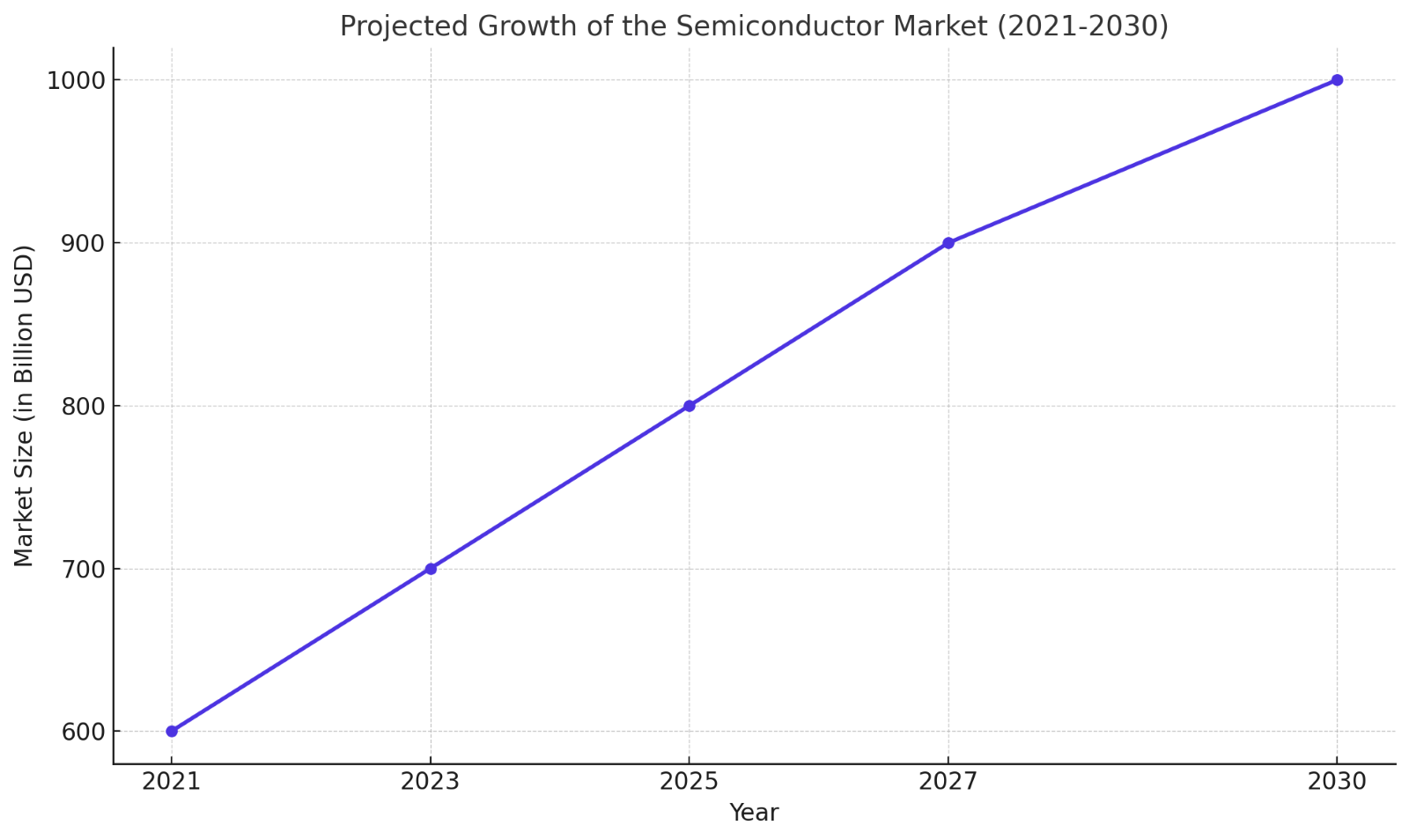
As detailed in our CHIPS and Science Act summary, governments and major corporations worldwide are engaged in a high-stakes race to meet the surging demand for semiconductor chips. The U.S. government has pledged $260 billion to domestic projects, while the European Union has committed $47 billion to bolster its semiconductor industry, and Japan has allocated $6.8 billion. However, this rapid expansion is not without challenges. In Europe, funding efforts face hurdles such as fragmented decision-making and an uncertain economic environment that could complicate long-term commitments. The market’s cyclical nature—of high demand and supply gluts—further underscores the complexity of scaling up investments sustainably. Despite these challenges, the push to secure a resilient semiconductor supply chain is reshaping the global economy and driving fierce competition.
This extraordinary growth comes with significant challenges, particularly in constructing fabs required to meet such unprecedented demand.
Digital transformation stands at the heart of addressing these challenges, offering innovative solutions to streamline processes, reduce costs, and drive the industry forward.
Semiconductor Supply Challenges
Imagine a world where every aspect of modern life—from healthcare innovations to AI-powered solutions—grinds to a halt because the tiny chips that make it all possible are in short supply. This isn’t a far-fetched scenario but a reality we narrowly avoided during the global chip shortage. Countries around the world are pouring tens of billions of dollars into semiconductor manufacturing, but these billions can quickly be wasted in the construction process.
Building a semiconductor fab is a high-wire act; it demands flawless coordination of utility designs, systems integration, and global supply chains. Even a minor misstep—like delays in installing power infrastructure—can cascade into millions of dollars in added costs and months of project delays.
Take a $28 billion dollar semiconductor fab project in Ohio as a case study.
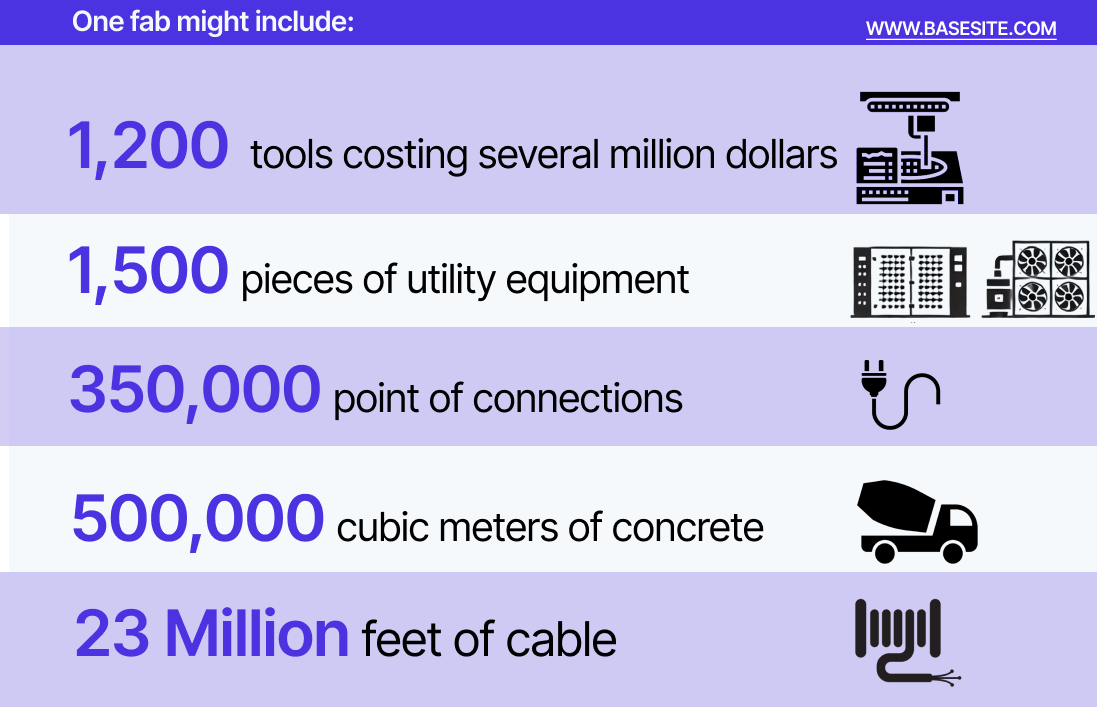
A break down from our 2025 AI and automation report reveals how complex a fab construction project can be. While promising to create 3,000 permanent jobs and 7,000 construction roles, this project is as ambitious as it is complex. It’s the epitome of the industry’s broader challenges: astronomical costs, tight timelines, and a critical shortage of skilled talent. Yet, despite these hurdles, projects like Intel’s prove that innovation can overcome adversity. With so much at stake, leveraging digital transformation tools to streamline processes, predict risks, and reduce waste is no longer optional—it’s essential.
Digital Transformation in Action
How do you combat rising complexities and costs in semiconductor fab construction? Enter digital transformation. While the potential of digital transformation spans across various facets of semiconductor manufacturing, this section focuses on a few targeted use cases in the construction phase—where complexities and inefficiencies often reach their peak.
Optimize Tool Layouts in Days, Not Months
Traditional tool layout designs often require months of back-and-forth manual effort, leaving room for inefficiencies. Our platform leverages advanced algorithms to identify the optimal layout configuration while balancing equipment placement with utility demands. This approach not only cuts weeks off timelines but also reduces errors, prevents material overscoping, and minimizes waste.
Track Every POC Efficiently
Modern semiconductor fabs can house up to 2,000 tools, creating thousands of Points of Connection (POCs) that must be meticulously tracked and managed. Despite this complexity, unreliable manual processes remain the norm. With AI-driven solutions, real-time tracking and management of POCs become seamless, ensuring each connection is fully utilized and precisely mapped. This bird's-eye view minimizes overlooked gaps and eliminates costly rework during construction phases.
Make Confident, Data-Driven Decisions
Without a single source of truth or centralized data, the risk of errors, delays, and non-compliance skyrockets during construction and installation. Improper planning or installation can lead to safety hazards and failure to meet environmental regulations. Digital transformation tools provide a single source of truth, enabling accurate, real-time records accessible to all stakeholders. This creates a safe, efficient setup that saves money, reduces risks, and accelerates timelines.
Automate Workflows to Stay On Budget and On Time
By automating workflows, digital transformation eliminates redundant tasks, streamlines communications, and ensures compliance with industry standards. This holistic approach enables projects to stay under budget and ahead of schedule while maintaining the highest quality standards.
These innovations, supported by insights like those in McKinsey’s Semiconductor Decade Report, are enabling fabs to be built faster, more cost-effectively, and with fewer disruptions.
Bridging Innovation with Results
The promising benefits of digital transformation lie not only in its ability to address industry-wide challenges but also in its practical application. As the semiconductor industry embraces this new era of facility optimization, the focus shifts to identifying the technologies and partners capable of turning potential into measurable results. So, what does this type of digital transformation look like?
From creating unified data frameworks to automating workflows, digital transformation technologies provide the tools engineers need to overcome complexity and improve efficiency.
Basesite supports owners by delivering solutions that streamline workflows, reduce costs, and empower teams to tackle even the most complex fab construction projects. Through its advanced tools, Basesite ensures semiconductor manufacturers have the resources to rise to these challenges.
Basesite’s Unique Value in the Semiconductor Expansion
“Digital transformation is about giving people the right tools for the scale of the job.” – Donal Murtagh, Basesite Director of Engineering.
In an industry defined by high stakes and tight timelines, the right tools are essential for overcoming challenges highlighted in the Global Semiconductor Outlook by Deloitte. By addressing the critical pain points of fab construction, Basesite helps semiconductor manufacturers translate the potential of digital transformation into actionable results.
- Messy Data Management: The complexity of fab construction often leads to fragmented and inconsistent data, resulting in inefficiencies and costly errors. Basesite creates a unified, reliable data framework—a “single source of truth”—enabling seamless collaboration and accurate, real-time decision-making.
- Streamlining Workflows: Disconnected teams and outdated manual processes can derail even the most meticulously planned projects. Basesite integrates siloed teams with automated workflows, ensuring projects remain under budget and on schedule.
Delivering Tangible Results:
- 40% faster GAP assessments, enabling teams to anticipate and resolve issues with unprecedented speed
- $3.5 million saved by reallocating engineering resources to higher-value tasks, cutting waste and boosting productivity.
For more insights, explore Basesite’s Case Studies, showcasing how these solutions have transformed fab construction through significant time and cost savings.
The Future: A $1 Trillion Market by 2030
The semiconductor industry is poised for extraordinary growth, with the market projected to reach $1 trillion by 2030. Reports like McKinsey’s Semiconductor Decade emphasize that this success hinges on scaling fab construction and achieving operational efficiency. The industry must navigate key drivers such as:
- Demand from Emerging Industries: AI, EVs, and IoT are pushing the limits of semiconductor production, demanding faster, more efficient solutions.
- Operational Scalability: Advanced digital tools ensure fabs can adapt to surging demand while controlling costs and reducing environmental impacts.
Digital transformation will be the cornerstone of this growth, providing the tools and strategies companies need to scale effectively, innovate, and lead the charge toward a sustainable future.
Conclusion
Securing a sustainable semiconductor supply is no easy feat—it requires seamless coordination between public and private sectors. Governments must continue investing in infrastructure and innovation, while companies leverage transformative technologies to meet the rising demand for chips across industries.
As the industry works toward the projected $1 trillion target by 2030, digital transformation will serve as the rocket propelling it forward. By embracing innovation, streamlining operations, and fostering collaboration, the semiconductor industry is poised to redefine the future of technology and drive global progress for decades to come.