IN FOCUS: The real impact of basesite’s design automation tool
We built our facility optimizer tool specifically to make the process of designing advanced manufacturing facilities more efficient and cost-effective.
Drawing on years of experience in the field, we built a solution that makes a substantial difference, reducing costs and cutting down on the “overscoping” of materials.
But how do our outputs really compare to the traditional manual approach, and what could that mean for your next build?
Comparing basesite against the manual approach
As seasoned engineers, our founding team is familiar with the process of designing the layout of a modern Sub Fab facility. Our tool uses technology such as proprietary optimization algorithms to make this process easier, while still delivering trustworthy results.
This solution is already trusted by owners and contractors in seven countries. However, we recently took the opportunity to test it directly against the manual outputs produced for a 300mm fab project in the USA.
We believe the results speak for themselves.
Addressing issues in the Sub Fab fit out process
When it comes to designing Sub Fab facilities, today’s engineers do an exceptional job handling a very complex problem.
However, the human brain isn’t ideally suited to a problem of this type. Those tasked with this design must find the optimal way to connect as many as 1,000 electrical panels, 2,000 process laterals, and 500 chemical cabinets, connected by as many as 200,000 cables and pipes. They must consider client and industry specifications, optimize space and cost, and bear in mind factors such as redundancy and the lead times for ordering materials.
Designs can take time, and plans can change in the meantime. Therefore engineers traditionally add a little buffer into their scope to accommodate any alterations during the process. This can mean that companies end up paying for more than they require, adding extra cost to an already-expensive process. For example, on previous projects, the manual electrical design had many panels loaded to just 20% of their capacity.
Our solution enables companies to receive an optimized design in a shorter time period. This design can be tailored to meet the needs of the tool set, and - if required - a buffer can be applied to provide more flexibility.
As results can be generated far more quickly, it means that the design can react to any changes that are required within a matter of days.
An opportunity to test in the field
After a couple of successful tests against completed designs, we were recently asked to run a proof of concept project at a 300mm facility being built in North America.
While a manual design had already been commissioned for the project, the client was keen to see how our tool could perform in providing a facilities scope for selected electrical, mechanical and Bulk Chemical Distribution Systems (BCDS).
Over the course of four weeks, we engaged with the client to gather the required information. As the tool would be compared against the manual design, we needed to ensure we were working toward the same design criteria and assumptions.
We established layout criteria, which confirmed where we could place laterals, panels and cabinets. We also received and cleaned all the data we needed, including layouts, tools details, and facility architectural details.
This enabled our specialized algorithms to provide a list of panels, laterals and cabinets with their optimal locations, as well as a PowerBI report for electrical outputs, allowing the client to drill down into the results.
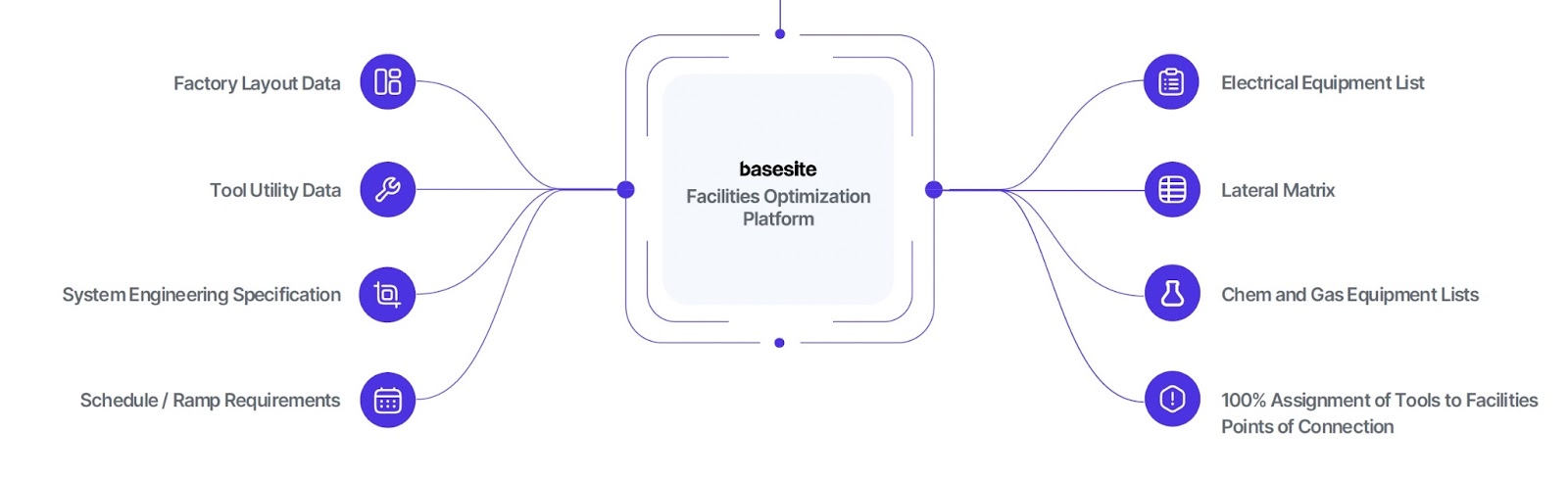
The basesite advantage
Within a short period of time, we were able to produce a design that would reduce the number of panels and the length of cables required.
The test demonstrated that the company could save a significant amount of money on cable and panel costs by adopting our approach, and reduce the need for “overscoping”. Furthermore, the speed at which these outputs could be produced would provide the company with significant advantages in a competitive field.
For a critical early design release for long lead equipment and long lead material, a manual design process would take around 6 weeks. Basesite’s automated design process could be completed in as little as a week.
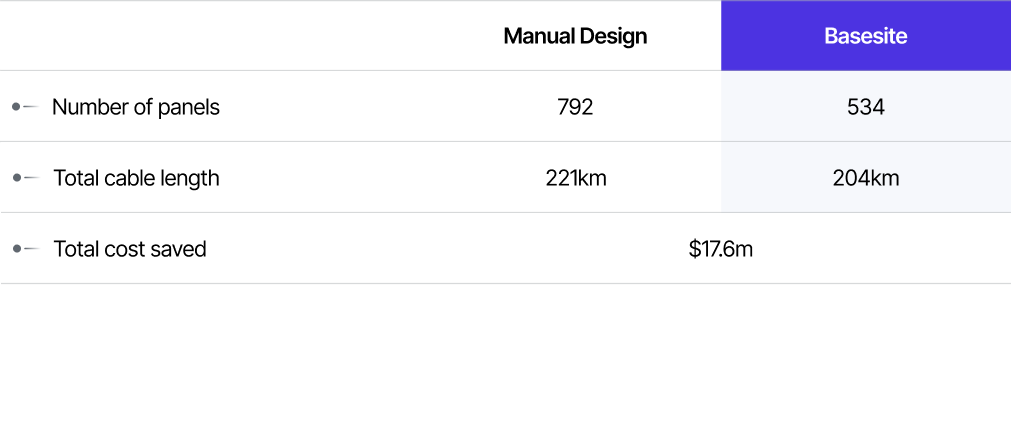
Following implementation, we are now rolling out this approach at other sites around the world.
“Working with this approach drives efficiency and savings - not just in scope but also in schedule and resources.
“Ultimately, it gives clients the ability to order and streamline engineering data, as well as to “optioneer” different designs based on varying criteria. With these advantages, the possibilities are manifold.”
Brian Culhane, CEO, basesite
A new way to optimize your Sub Fab design?
So how can results like this impact your next Sub Fab design?
Our optimization algorithms are ideally suited to the kind of calculations required in the design process. They can analyze millions of data points to connect your facility in the optimum way, and even test multiple different options simultaneously against one another based on your specifications.
This reduces the need for a long design process, saving you and your engineers time. Our tool can also take into account factors such as redundancy, and reduces the need to order more materials in case of errors or changes.
basesite enables companies to deliver results that are quick, efficient, reliable and optimized. This means they can reduce costs, build quicker, and assign talented engineers to the jobs where they can make the greatest impact.