How a 300mm Fab in EMEA Saved $30 Million by Fixing the Hidden Costs of Tool Installs
The Real Impact of Basesite’s Facility Connect Platform
Facility Connect was built by engineers who’ve felt the pain of delayed ramps, misaligned installs, and last-minute surprises during facility changes. We knew there had to be a better way, so we built one.
Our platform digitizes and streamlines the process of managing tool-to-facility connections, helping engineering and construction teams stay in control during every install, expansion, and retrofit.
This case study shows just how transformative Facility Connect can be when deployed at scale.
Managing Change at Scale: A 4-Year Project, 2,500+ Tools, and 12,000 Modifications
A global semiconductor manufacturer deployed Facility Connect during the construction of a new 300mm fab in EMEA. Over four years, the team needed to manage:
- 2,535 tools
- 350,000 points of connection (POCs)
- 12,000 change events
In a facility with this level of complexity, every manual process becomes a bottleneck, every spreadsheet a risk.
The Real Cost of Manual POC Management
Each tool in the fab requires dozens of connections; mechanical, electrical, exhaust, gases, all of which must be manually assigned, coordinated, and updated every time scope changes.
Another major time sink? Pulling together the drawings and documentation needed to install each tool (Tool Package Creation) This includes compiling sheets from multiple reference sources to tailor them for the tool’s specific location in the fab, a time-consuming task repeated thousands of times.
Here’s a breakdown of where time was lost per medium-complexity tool:
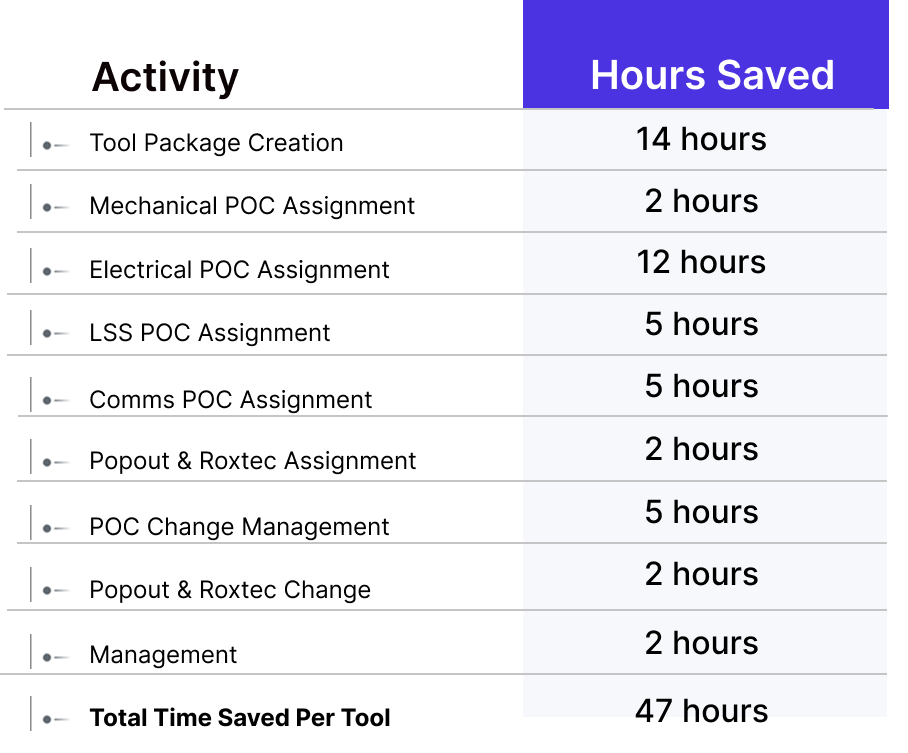
Multiply that across 2,535 tools, and the labor savings alone reach thousands of hours.
The Estimated Impact: $30 Million Saved
By digitizing tool and facility data, automating POC assignments, and enabling real-time visibility into system constraints and embedded risks, Facility Connect helped the project team save an estimated:
$30 million over four years
= $7.5 million per year
This included both direct labor savings and avoided costs from rework, scope creep, and unplanned delays.
Why It Matters
In high-complexity fabs, scope gaps often surface late in the process, just before a tool is due to be installed. These gaps happen when connections are missed, system capacity is misjudged, or design assumptions don’t match the real-world conditions on site.
When that happens, teams are forced to pause installs, scramble for redesigns, or request additional budget. Adding weeks to schedules and millions to project costs.
Facility Connect changes that. By giving teams real-time visibility into system constraints and embedded risks, and by digitizing the entire POC process, gap analysis happens in days, not months, and scope misalignments are caught early and before they impact delivery.
A Smarter Way to Manage Facility Change
If your team is building or modifying high-complexity manufacturing environments, Facility Connect helps you:
- Avoid downtime and ramp delays
- Automate manual, error-prone processes
- Plan with confidence using real-time data
- Scale faster with fewer surprises
Whether you’re managing thousands of tools or coordinating across disciplines, Facility Connect gives you the control and clarity you need to deliver on time and on budget.